COVID-19 made the world completely rethink how to manage supply chains. But supply chain disruptions are nothing new, they have always occurred, and we were never well-prepared for them. It’s time to make lasting changes to global supply chains using the technology tools we have now.
Mounting supply chain disruptions
The New Yorker once again asks an important question: ‘Why do strange shortages keep on popping up in our lives more and more?’ Everything from rental cars, plumbing fixtures, and even salad dressing — most of us have been waiting far longer than usual for our deliveries and shipments. While our shelves are not completely empty yet, and though we can cope with a shortage of a special kind of pasta — or three-times-as-long delivery waits for new windows, as I have experienced — Amy Davidson Sorkin rightfully poses a bold statement:
There is “something off with the way we’re operating in the world,” and we do not yet “know the extent of our vulnerabilities.”
Just last week, the White House, concerned that semiconductor supply chain shortages specifically could drag down the entire US economy, outlined federal goals to prevent and address further supply chain disruptions. The US Department of Commerce said that among the goals are to build supply-chain “trust” and reduce dependency on vulnerable supplies.
What is the culprit of these massive disruptions? It's not just COVID-19
COVID-19 has led supply chains to go out of sync — in some cases due to bullwhip effects, in other cases, pure disruptions due to lockdowns. It will take a long time to recover — 12 months, or even longer, the experts say. Let’s look at some of the driving forces for supply chains going out of sync:
➡ As data from the Altana Atlas show and as we lay out in the whitepaper Making Your Supply Chain Shock Proof, the auto industry, as one example, was not able to cope with the strong return in demand following a pause in consumers purchasing cars at the start of the pandemic — especially as the consumer tech industry had gulped up the capacity to produce the semiconductors that are crucial to both industries.
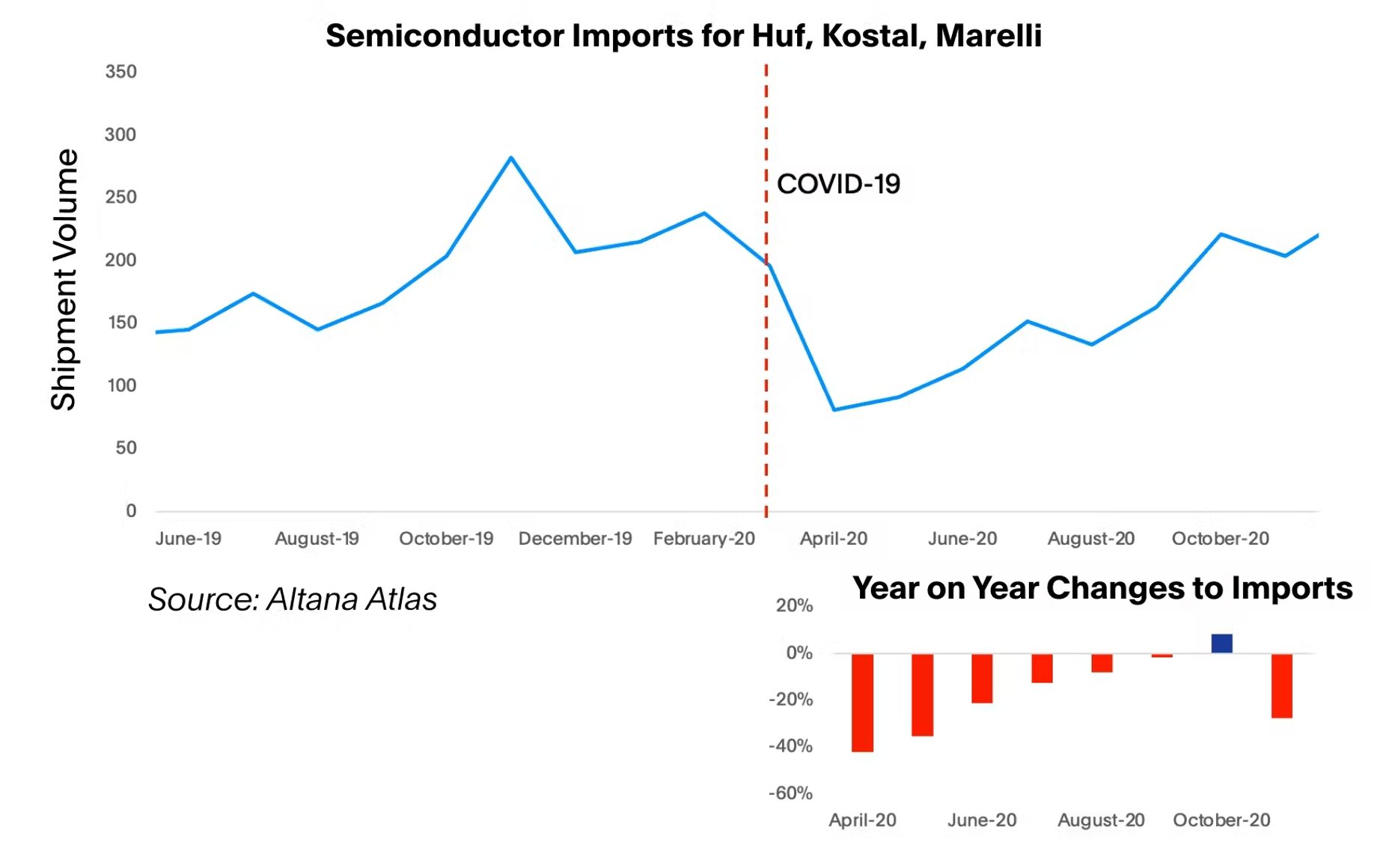
Above, Altana Atlas data from our whitepaper shows that a deficit in imports from early in the COVID-19 pandemic seeded the foundation for supply chain disruptions further downstream.
➡ Freight Waves writes that the American stimulus package also gave consumers renewed purchasing power, shifting buying behavior from purchasing services to physical products, which bought up trillions of dollars of inventory while the domestic and global production of products was shut down.
➡ Then, there is the debated labor situation. The logistics industry has notoriously struggled to attract talented drivers. As the rise of e-commerce demands quick and cheap movement of goods, low pay has led to a “massive degradation in the quality of work,” as Steve Viscelli explains in his book, The Big Rig. With COVID, the problem has exacerbated and peaked across many professions required to keep goods moving, not only for drivers but also port operators and warehouse workers. Workers are not returning after being laid off during the pandemic or are searching for more attractive work away from the transportation industry.
➡ Further compounding the issue are climate-related disasters. Adding to the most recent concerns reported by the WSJ are power outages at key Chinese manufacturing hubs due to government efforts to curb energy consumption and surging prices for coal.
It's important to note, though: COVID-19 has not been the sole driver of the resounding, multiple failures of our supply chains. For the most part - historically - supply chain leaders sought cost optimizations versus resilience. Already in 2011, the world dealt with a 'black swan' event, but only a few companies learned the lesson, with Toyota being one of the exceptions. Supply chain issues have always existed, but only now, as so many of our purchases, big and small, are caught up in delivery limbo, is the entire world paying full attention. All things considered, before COVID-19, it may have been difficult to economically justify all the contingencies needed to handle a disruption on this scale. Now, the cost baseline for many industries may be changing.
Industry shifts focus
At the recent Council of Supply Chain Management Professionals 2021 conference, almost every session confirmed a shift from Just-in-Time to Just-in-Case supply chains. We believe it is evident that we must completely refactor global supply chains to react to the modern-day chokeholds of commerce: Supply chain leaders need visibility beyond their first tiers of suppliers, consumers demand product traceability, our society wants to track end-to-end carbon emissions, and lastly, our economies should take further steps to lessen income inequalities along the value chains that produce the products we desire.
With the recent announcement of Altana AI’s Series A investment, our CEO Evan Smith painted a picture of what “Globalization 2.0” could look like — and how more visibility into our supply chains through shared intelligence and AI is the right vehicle to get us there. In our future blogs, we will discuss if these recent events are a catalyst for more permanent change, or if this focus on resilience is yet again a temporary phenomenon.